Screen
printing is one of those things that I think everyone, artist or not,
should learn to do. It's a cheap, easy (and fun!) way to create a bunch
of awesome, identical copies of whatever you want. Screen printing is
one of the most versatile printmaking processes out there - you can
screen print anything from paper (like I'm going to show you how to do)
to glass or computer chips. In this thread I'll show you how to print
posters, but you can take this information and apply it to most other
things, like shirts or whatever you want.
I know this post is long and it seems complicated, but it's actually really easy and doesn't take much time.
This poster is one I'm printing for a friend's fashion show, it's not
done but it will be later tonight I think, I'll post pics of the
finished ones later. I'm taking a break from working on final projects
to do this and haven't slept in a while, so excuse me if some of this
doesn't make sense, and feel free to ask questions if something's not
clear.
WHAT IT IS
Screen printing is the process of pushing ink through a stencil (that's
adhered to a fine mesh) to create perfect, identical copies. There are
various ways of making the stencil, the method I'm going to explain
uses photo-emulsion and is the easiest and least labor intense.
SUPPLIES
When I say you can screen print for cheap, I mean
cheap.
I know someone, who enjoys pain, who screen printed by stretching panty
hose over an embroidery loom and used glue to make his stencil. I don't
recommend that, especially when professional supplies don't cost much.
Yes, you can go down to your local art store and pay a shit load for
extremely crappy quality supplies. Yes, you can buy one of those
terrible, terrible Speedball kits. That stuff will work (barely and
probably with way more problems than if you used real supplies), but I
guarantee if you're going to do this more than once that stuff will be
useless after doing your first run of prints. I'm going to list what
you need, and also where I recommend buying it from (I'm not getting a
commission or anything, these are just places I've had experience with).
-
A screen - A screen consists of a frame and mesh. There
are various types of frames, wood being the cheapest and shittiest. You
should go with an aluminum frame (won't warp, holds better
registration, keeps mesh tighter/longer, more durable, etc.), they're
usually a tiny bit more expensive than wood but they're definitely
worth it. Mesh comes in various "sizes" which refer to how many threads
are in it. The higher the number, the less ink gets put down and the
more detail the screen can hold. For posters, you want 200 or 230 mesh.
Note that for shirts and other things 110 is pretty standard. Remember
that you need at least 4-6" around your image area, and that screen
measurements are the outside dimension, not the usable inside portion.
Example: for my 12x18 posters, I use 23x31 screens.
I recommend: Aluminum screens with 200 mesh from
www.rhemadurascreen.com
-
a squeegee - This is what you will use to push the ink
through the mesh. There's a handle and a blade. The blades come in
different hardnesses, if you have a choice when buying one just get 70
but it's not really important. Squeegees are about $1 per inch, and you
need one that is at least 2 inches bigger than your image. Example: for
my 12x18 posters, I use a 14" squeegee.
I recommend:
www.rhemadurascreen.com or
www.victoryfactory.com
- (
OPTIONAL)
scoop coater - These are nifty and if
you think you'll be doing this more than once get one, they spread your
emulsion on the screen quickly and evenly.
I recommend: rhemadurascreen.com has the nicest ones i've used by far.
-
emulsion - Emulsion is a light sensitive liquid that you spread on your screen. This is what makes the magic happen.
I recommend: Ulano QTX from
www.valleylitho.com
-
stuff to expose - To expose your screen, you need a
clamping work light, a 150 watt light bulb, some sort of rod (like a
shower curtain rod), two chairs/stools, a piece of paper/cardboard
spray painted matte black (NOT glossy black), your artwork printed on
either a transparency or vellum, and (optional but recommended) a piece
of glass as big as your image.
-
jiffy clamps - these bolt down to a table or other
surface and then clamp your screen in place. You need a set of two, and
should be able to get them from any of the places I've listed so far.
-
paper - Any 80 or 100lb cover stock will be good for posters.
I recommend:
www.mrfrench.com is awesome, cheap, and archival. Or just go to xpedx or something.
-
ink - They make all kinds of inks for use on paper.
Basically, you can use pretty much anything. Speedball Acrylic screen
printing inks are the only Speedball product that doesn't suck loads of
ass and they come in a lot of colors. Any waterbased screen printing
ink is fine. Once you get the hang of printing, you can switch to using
latex housepaint, which is like $1/qt from the mistint rack at Lowe's
and Home Depot.
I recommend: any ink from
www.valleylitho.com or
www.dickblick.com
(ONLY GET INK FROM THEM! everything else they have is crap!). water
based is a lot easier to clean up than solvent based, so get that.
HOW IT WORKS
Step 1: Take your brand new screen and degrease it. You can buy fancy
degreaser, but I think that's pointless since dishwashing liquid works
fine ("tough on grease, not on your hands!"). Just rub it in and then
wash it off.
Step 2: Once it's dry, you need to coat your screen with emulsion. If
you've got a scoop coater, just pour the emulsion in it, position the
screen vertically, and spread it on. If you don't have one, try to
spread it as evenly as possible on your screen using your squeegee.
Step 3: Let the emulsion dry. Store you screen somewhere dark
(remember, it's light sensitive!). Make sure you are storing it
horizontally with the print side down (in the picture below, the print
side is facing the camera). Put a can of soup or something under each
corner in your bathroom overnight, that'll work great.
When it's dry, it'll look like this:
Step 4: Time to expose your screen. You need a print out of your
artwork on either transparency or vellum (make sure the ink is opaque
as possible). You need a seperate screen and a seperate positive for
every color. Take two chairs or stools, and put a shower curtain rod
over the back of them. Clamp your light to the rod. Put your piece of
paper that's matte black on the floor, and then put the screen on top
of that with the print side up. Place your print out (this is called a
'positive') REVERSED on top of the screen, and then put a piece of
glass on top of that to hold it flat (don't use UV blocking glass).
Then just turn the light on. Your emulsion will come with instructions that will tell you how long you need to expose it for.
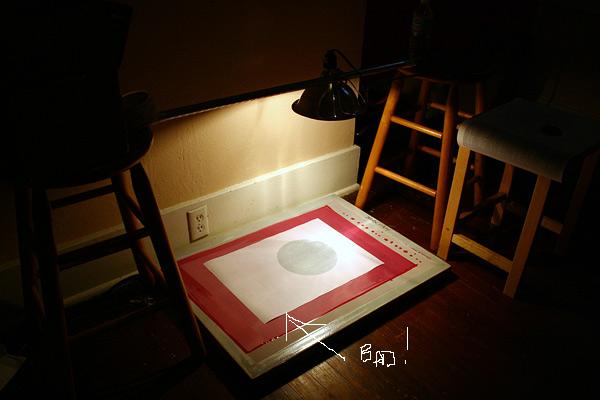
i broke my piece of glass last week, see how the positive isn't laying
flat? that's bad. for this screen it didn't matter, for the final
screen with text it did. a lot.
What happens is that everywhere light hits the emulsion, it becomes
water resistant. Obviously, where there's black on your positive the
light doesn't hit it, so that brings us to the next step.
Step 5: Wash out. Take your screen into your shower (or outside AT
NIGHT - it's still light sensitive! - if you want to use your hose) and
gently wash it out with water. Wet both sides, and then spray it down
from the inside of the screen, like this:
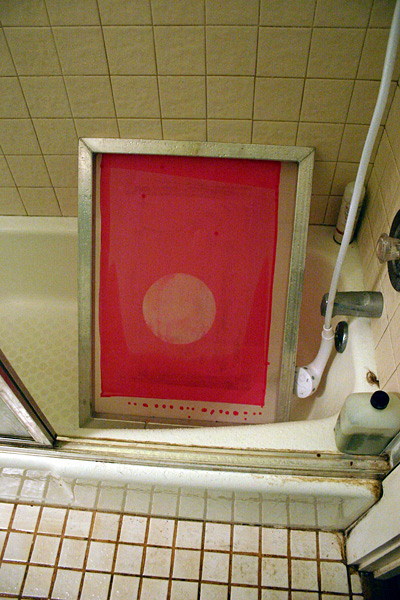
This is about halfway washed out. Before you stop, hold the screen up
to the light and make sure no emulsion remains in your image area. If
you overexpose it, it won't wash out all the way. If you underexpose
it, all the emulsion will break down and come off.
Step 6: Dry it out. Box fans = good.
Step 7: When it's dry, we're almost ready to print. Now we have to get everything registered.
Getting the screen lined up to print in the right spot is called
registration. First, tape your positive down along one edge to your
print area. For the first color, line up the screen to the positive,
and then lock the screen down with the clamps. When I do posters I
always get a print of what it should look like with all the colors down
for registration, like so:
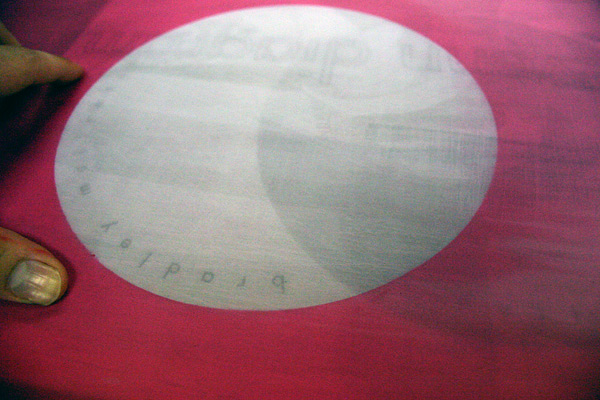
It's hard to see in this picture, but you'll be able to see through the mesh to line up your screen to your artwork.
Ok, know how we only taped down one edge of the positive? Lift up your
screen and slide a piece of your paper underneath it and line it up
where you wanted it printed on the paper. Now very carefully remove the
positive so that just your piece of paper is on your print surface in
the right spot.
Step 8: So you've got your paper in the right spot on your print
surface, but you want to print 100, not 1! how do you get all your
paper in that exact same spot?
This is called three point register. You take two tabs of cardboard (or
anything, as long as it's thicker than what you're printing on) and put
those along one corner, and then another tab all the way at the end of
the longest side. Now you just slide each piece of paper into these
tabs for every sheet you print.
Also, see that paint stirrer thing taped down? This is to mantain "off
contact". Your screen should be about 1/8" up from the surface of what
you're printing on. The jiffy clamps will hold it up that much on the
other end, you need to prop it up a little on this end though.
Step 9: Almost fucking ready to print.
Tape up the edges to your screen so that ink doesn't leak through. Put
your squeegee on the opposite end from where you'll be printing.
Optional Step 9.5: Using a counterweight on your screen helps
immensely. Basically, you put a C-clamp on the end of your screen (as
seen above) that is tied to a string. This string has some sort of
weight attached to it at the other end, and mine goes up through a hook
in the ceiling. The weight should be roughly equal to the weight of
your screen and your squeegee. If you do this, between prints you just
lift the screen up and it stays up. If you don't do this, you'll have
to stick something under it to prop the screen up while you switch the
paper out.
Here's a better picture of the counterweight:
Step 10: Now we're finally ready to print.
Put some ink on your screen. Always try to keep just enough on there to
print with, otherwise it'll get messy and the ink will run everywhere.
Just add more as you need it.
Now, how do you fucking print? There's two parts to printing, first you
do what's called a flood stroke. Keeping the squeegee at about a 60
degree angle, and using minimal to no pressure, pull the ink towards
you to cover the image area with ink. Do this while the screen is
raised from the paper.
Flood stroke:
See how now your image area is filled with ink? Next step is the print
stroke to lay that ink down on your paper. Lower the screen, and using
even pressure (and keeping the squeegee at a 60 degree angle) go back
across the image. You can either "pull" the squeegee towards you like
you did with the flood stroke, or "push" it going the opposite way.
Either way works and neither is more correct than the other.
Run off some test prints to get the ink flowing through the screen
before you start on your good paper. I usually use newsprint, or here I
used a misprint from a past run:
(Note: I thinned these inks down a lot to make them transparent, yours will be opaque)
Repeat that 60 times and we get:
Step 11: Ok great, but obviously most posters will be more than one
color. How do we register the other ones so that all the colors are in
the same spot on every poster? This is how I do it:
Tape your positive down again, just like you did for the first color.
Line your screen up to it and clamp it in. So far we haven't done
anything different than what we did with the first color.
Now, take one of your prints and slide it under your positive. Line it up, like so:
Take the positive off, put down your 3 registration tabs, and we're ready to go.
and repeat it again:
I've got one more color to go on this, which I'll do tomorrow.
When you're done with your screens, you can reuse them. Get a chemical
called - amazingly - emulsion remover and it will make your screen as
good as new.
Also, you don't want your paper to stick to the bottom of you screen
after you print. The table in those pictures is a vacuum table i built,
which uses a rigged up vacuum cleaner to hold the paper down. You can
just use spray adhesive on your printing surface instead, that will
work fine.
Hopefully I didn't leave anything out. I own/work in my screen printing
shop every day, so if you have any questions about screen printing I
can probably answer them.
EDIT:
plans for the vacuum table in those pictures are here: http://www.tenfortyfive.org/vacuumtable/